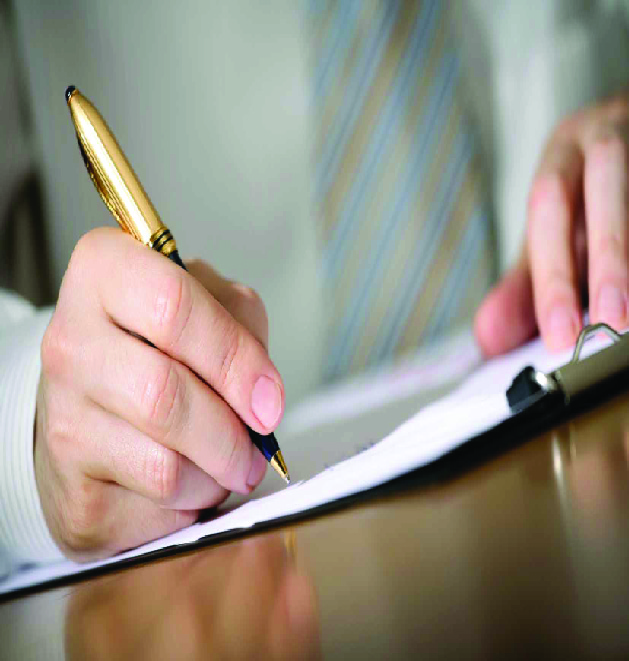
TPM
Total productive maintenance (TPM) is the process of using machines, equipment, employees and supporting processes to maintain and improve the integrity of production and the quality of systems.
TPM (Total Productive Maintenance) is a holistic approach to equipment maintenance that strives to achieve perfect production:
- No Breakdowns
- No Small Stops or Slow Running
- No Defects
In addition it values a safe working environment:
- No Accidents
TPM emphasizes proactive and preventative maintenance to maximize the operational efficiency of equipment. It blurs the distinction between the roles of production and maintenance by placing a strong emphasis on empowering operators to help maintain their equipment.
The implementation of a TPM program creates a shared responsibility for equipment that encourages greater involvement by plant floor workers. In the right environment this can be very effective in improving productivity (increasing up time, reducing cycle times, and eliminating defects).
Going from reactive to predictive maintenance is one of the biggest advantages of implementing a TPM program. Reactive maintenance or “firefighting” is costly, as you’re not only footing the bill for machinery repairs but also dealing with the cost of unplanned downtime. Let’s take a look at some of the direct and indirect benefits that result from total productive maintenance.